Металорізальний інструмент
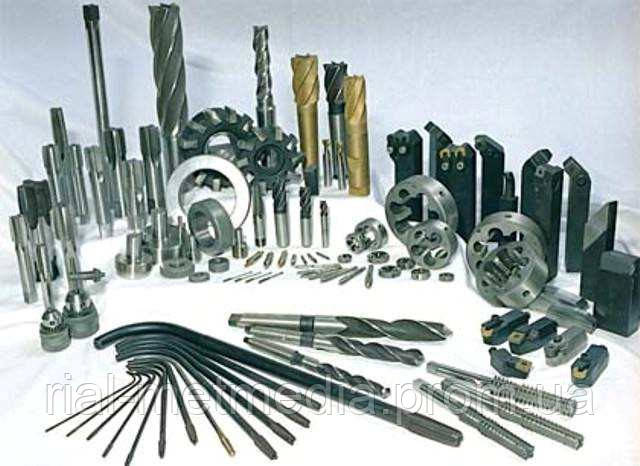
Металорізальний інструмент є одним із найважливіших знарядь виробництва. Він використовується при обробці різанням всіляких деталей на металорізальних верстатах. При цьому зрізається частина матеріалу заготовки у вигляді стружки до отримання необхідної поверхні деталі.
В даний час у машинобудуванні використовується велика кількість різноманітних ріжучих інструментів.
На зорі розвитку людської культури одними з перших знарядь, якими користувалися люди в процесі своєї праці, були кам'яні знаряддя. Вже в епоху неоліту людина досяг великої майстерності у виготовленні найрізноманітніших кам'яних знарядь: скребків, різців, наконечників, голок, кинджалів, сокир, молотків, доліт, мотик, серпів, напилків.
Кам'яні знаряддя були крихкими, вони часто ламалися, а расширявшаяся виробнича діяльність людей вимагала більш міцних знарядь. Тому в 3-1 тисячоліття до н. е. на зміну каменю прийшли мідь, олово і бронза. Знаряддя, виготовлені з бронзи, були міцними, але їм бракувало твердості і гостроти кам'яного знаряддя. Тому бронза не могла витіснити кам'яні знаряддя.
Розвиток ремесла настійно вимагало створення такого матеріалу, який поєднував би в собі міцність бронзи і твердість каменю. Таким матеріалом стало залізо. Воно дало реміснику знаряддя такої твердості і гостроти, яким не міг протистояти жоден камінь, жоден з відомих тоді металів.
Різкий стрибок у розвитку продуктивних сил суспільства ми спостерігаємо при переході від мануфактурного виробництва до машинної індустрії, це було пов'язано з переходом від ручної праці до машинної, з передачею функцій механізму безпосереднього впливу на предмет праці.
Перехід до машинної індустрії призвів до надзвичайно бурхливого розвитку інструментів і створення нових їх типів.
У другій половині XIX століття з'являються такі інструменти, як спіральне свердло, розгортка, зенкер, різноманітні фрези, в тому числі затыло-ванні фасонні фрези для обробки зубчастих коліс. В кінці XIX і початку XX століть стали використовуватися у виробництві такі складні інструменти, як черв'ячні фрези, зуборізні долбяки, гребінки та ін Двадцяті роки XX століття характеризуються впровадженням такого інструменту, як протяжка, яка в даний час знаходить широке застосування в силу високої продуктивності і якості обробки. В цей же період починають застосовувати всілякі об'єднані інструменти, набори інструментів, що дозволяють поєднувати різні операції.
Ріжучий інструмент є найважливішим елементом техніки різних галузей машинобудівної промисловості. Протягом всієї історії техніки вдосконалення ріжучого інструменту чинили великий вплив на конструкцію металорізальних верстатів і технологію машинобудування.
Успішний розвиток будь-якого машинобудівного виробництва в значній мірі залежить від того, наскільки воно забезпечене належним кількістю високоякісного інструменту.
Одним з найбільш простих і розповсюджених металорізальних інструментів є різець. Різці застосовуються на токарних, розточувальних,строгальних і інших верстатах. В залежності від виду верстату і виду виконуваної роботи застосовуються різці різних типів. Нижче зображені основні типи токарних різців.
Крім прохідних токарних різців широке поширення отримали підрізні, розточувальні і відрізні різці.
Підрізні різці виготовляють з відігнутою і прямий державками. Хоча відігнута державка ускладнює виготовлення різців, вона забезпечує наступні переваги: 1) універсальність, так як прохідні різці можуть працювати напроход і на підрізання ; 2) можливість вести обробку в менш доступних місцях.
Розточувальні різці використовують для обробки внутрішніх наскрізних і глухих отворів, а також внутрішніх канавок. З-за великого вильоту державки, зменшеної площі його перерізу і утрудненого відведення стружки розточувальні різці працюють в більш тяжких умовах, чим прохідні різці. Державки розточувальних різців виконують круглими, а в місці кріплення вони мають потовщення квадратного перерізу. Діаметр державки залежить від діаметру оброблюваного отвору і дорівнює dд = (0,5...0,8) dо, де do – діаметр оброблюваного отвору.
Розточувальні різці мають малу вібростійкість і жорсткість. Щоб виключити врізання задній поверхні різця в поверхню різання, лезо різця розташовують декілька нижче осі отвору, а задню поверхню виконують криволінійної форми.
Відрізні різці застосовують для відрізання заготовок з прутка і проточки зовнішніх канавок в заготовках на токарних, токарно-револьверних верстатах, верстатах-автоматах та ін.
Інструменти, оснащені СМП (твердосплавними змінними багатогранними пластинами) , порівняно з напайними, мають наступні переваги:
більш високі міцність, надійність і стійкість;
менші витрати на зміну та утилізацію пластин;
менші простої обладнання при заміні та налагодження інструменту, що особливо важливо при експлуатації сучасних дорогих верстатів з ЧПК і автоматичних ліній;
більш сприятливі умови для нанесення на пластини зносостійких покриттів, що дозволяє значно (до 4-5 разів) підвищити їх стійкість, а отже, і продуктивність процесу різання;
менші втрати гостродефіцитних матеріалів (вольфраму, кобальту, танталу та ін) за рахунок збільшення повернення пластин на переробку.
Недоліки інструментів, оснащених СМП:
висока вартість із-за їх високої точності, а отже, високу трудомісткість виготовлення пластин і інструменту в цілому;
підвищені габарити корпусів інструментів з-за необхідності розміщення в них елементів кріплення пластин;
неможливість повного забезпечення оптимальної геометрії ріжучої частини інструменту з-за заданої форми пластин і умов їх кріплення.
За кількістю ріжучих кромок і форм пластини мають різні виконання, закріплені в міжнародних і національних стандартах.
Геометричні параметри інструментів, оснащених СМП, визначають в статиці при виготовленні пластин і коригують при їх закріпленні в корпусі (державка) інструменту з урахуванням кінематики верстата і умов різання.
По геометричним параметрам СМП поділяються на: а) негативні (γ = 0°, α = 0°); б) позитивні (γ = 0°, α > 0°); в) негативно-позитивні (γ > 0°, α = 0°)
Задній кут при установці негативних і негативно-позитивних пластин створюється за рахунок їх повороту при кріпленні в державки різця. При цьому у негативних пластин передні кути стають від'ємними, тобто (–γ) = α, у негативно-позитивних пластин кут γ зменшується на величину кута α. У позитивних пластин кут γ дорівнює куту повороту пластини за годинниковою стрілкою, а кут α зменшується на цю ж величину.
Існує безліч конструкцій різців, що розрізняються за способом кріплення СМП, частина яких з метою зручності кріплення виготовляють з отворами. Аналіз численних конструктивних рішень кріплення пластин дозволив звести їх до наступних схем кріплення (по ІСО):
прихватом зверху;
важелем через отвір з притисненням до бічних стінок гнізда;
гвинтом з конічною голівкою;
штифтом через отвір і прихватом зверху.
Деякі приклади конструктивного виконання цих схем на різцях:
У різців найбільше поширення отримали пластини з отвором. Завдяки цьому забезпечуються вільний сходження стружки по передній поверхні і значно менші габарити елементів кріплення, що розміщуються в корпусі державки.
Різці, оснащені керамікою і синтетичними надтвердими матеріалами. Зазначені матеріали володіють високими твердістю, зносо - і теплостійкість, завдяки чому забезпечують значне підвищення продуктивності і стійкості, високі точність і якість обробленої поверхні. Їх недоліком є низька міцність ріжучого клина, яка обмежує область їх застосування. Найбільшу ефективність вони показали під час чистового точіння сталей, особливо загартованих, чавунів різної твердості і навіть твердих сплавів з вмістом кобальту вище 25 %. При цьому обробка повинна проводитися на високоточних, жорстких, швидкісних і потужних верстатах з ЧПУ останнього покоління.
Поставляється ріжуча кераміка у вигляді неперетачиваемых багатогранних пластин (ГОСТ 25003-81) круглої, квадратної, трикутної та ромбічної форми різних розмірів.
До групи надтвердих матеріалів, як вже зазначалося, відносять алмази (природні та синтетичні) та композити на основі полікристалів кубічного нітриду бору (ельбор).
Фасонні різці
Ці різці застосовуються для обробки тіл обертання, які мають зовнішні або внутрішні фасонні поверхні. Обробка цими різцями зазвичай ведеться на верстатах-автоматах та револьверних верстатах в умовах великосерійного або масового типу виробництва. В якості заготовок деталей найчастіше використовують калібрований прокат у вигляді прутка.
У порівнянні з іншими типами різців фасонні різці мають наступні переваги:
· забезпечують ідентичність форми деталі і високу точність розмірів, не залежить від кваліфікації робітника;
· володіють високою продуктивністю за рахунок великої довжини активної частини різальної кромки;
· мають великий запас на переточку;
· досить простого переточування з площини передньої грані;
· не вимагають великих витрат часу на налагодження та налаштування верстата.
До числа недоліків фасонних різців можна віднести:
· складність виготовлення і високу вартість;
· різці – спеціальні, так як вони придатні для виготовлення деталей тільки заданого профілю;
· великі радіальні навантаження у різців, які працюють з радіальною подачею, викликають вібрації і пружні деформації нежорстких заготовок, що вимагає зниження подачі і зменшує продуктивність;
· кінематичні передні і задні кути фасонних різців в процесі різання змінюються по довжині ріжучих кромок у великому діапазоні, істотно відрізняючись від оптимальних значень.
Свердла
Свердло являє собою ріжучий інструмент для обробки отворів в суцільному матеріалі, або для розсвердлювання отворів при двох одночасно відбуваються рухах: обертанні свердла навколо його осі і поступальний рух подачі вздовж осі інструменту. У промисловості застосовуються такі основні типи свердел: спіральні, перовые, гарматні, рушничні, для кільцевого свердління, центрувальні, спеціальні. Спіральне свердло є основним типом свердел, найбільш широко поширених в промисловості. Воно використовується при свердлінні і рассверливании отворів діаметром до 80 мм і забезпечує обробку отворів з 4-5-го класів точності і з чистотою поверхні 2-3-го класів. Перовые свердла є найбільш простими за конструкцією. Вони застосовуються при обробці твердих поковок, а також ступінчастих і фасонних отворів.
Особливості конструкції твердосплавних свердел
Незважаючи на те, що використання твердих сплавів забезпечує дво-, чотириразове підвищення продуктивності, питома вага твердосплавних свердел в загальному обсязі їх застосування становить не більше 10 %. Це пояснюється несприятливими умовами роботи твердих сплавів при свердлінні: нежорстких (консольних) кріпленням свердел; великими осьовими навантаженнями; змінною величиною швидкості різання, зменшується до нуля на поперечної ріжучої кромки; великою шириною срезаемой стружки; небезпекою появи вібрацій і пакетування стружки в канавках свердла; малими числами обертів і недостатніми потужністю, жорсткістю і точністю свердлильних верстатів. Більш широке поширення твердосплавні свердла отримали при свердлінні чавунів, кольорових металів і неметалічних матеріалів (мармур, цегла, пластмаси тощо). При свердлінні сталей часто спостерігається викришування різальних кромок, особливо у вигляді руйнування поперечної ріжучої кромки.
Зенкери
Зенкери - це осьові багатолезові ріжучі інструменти, які застосовуються для проміжної або кінцевої обробки отворів, отриманих попередньо свердлінням, литтям, куванням або штампуванням, з метою підвищення їх точності до JT11...JT10 і зменшення шорсткості обробленої поверхні до Ra 40.. 10. Зенкери отримали широке поширення в масовому і великосерійному виробництвах. Порівняно з расточными різцями вони, будучи вимірними інструментами, що не вимагають настроювання на розмір, що забезпечує скорочення допоміжного часу і підвищує точність отворів. Кінематика робочих рухів зенкеров подібна свердел. Однак порівняно з останніми зенкери забезпечують великі продуктивність обробки отворів і точність, так як знімають менші припуски (t = 1,5...4,0 мм, d = 18...80 мм), мають більшу кількість ріжучих кромок (z = 3...4) і направляючих стрічок. Із-за малої глибини стружкових канавок вони мають більшу, ніж свердла, жорсткість, а відсутність поперечної кромки дозволяє вести обробку з високими подачами. Зенкери класифікують за такими ознаками: по виду обробки - циліндричні зенкери (застосовуються для збільшення діаметра отворів,
зенковки (застосовуються для обробки циліндричних або конічних заглиблень під головки болтів, гвинтів, а також для зняття фасок) підрізування торців бобышек і припливів на корпусних деталях,
за способом кріплення зенкера -
хвостові (з циліндричним і конічним хвостовиком (d = 10...40 мм, z = 3)),
насадні (d = 32...80mm, z = 4);
цільні,
збірні (зі вставними ножами, d = 40... 120 мм),
регульовані по діаметру;
швидкорізальні,
твердосплавні.
по конструкції зенкера -
по виду ріжучого матеріалу -
Розгортки
Розгортання являє собою процес обробки отворів з метою отримання підвищеної чистоти і точності. Розгортка — це багатозубий інструмент, який подібно свердла і зенкеру в процесі обробки здійснює обертання навколо своєї осі (головний рух) і поступально переміщується вздовж осі, здійснюючи рух подачі. Розгортання дозволяє отримати отвір 2-3-го класу точності та 7-8-го класу чистоти обробленої поверхні. Кінематика робочих рухів при розгортанні подібна свердління і зенкерованию. На відміну від зенкеров, розгортки мають більше число зубів z = 6...14) і, як наслідок, краще напрям в отворі. Вони знімають значно менший припуск (t = 0,15...0,50 мм), ніж при зенкеровании. З метою досягнення мінімальної шорсткості поверхні розгортки при обробці сталей працюють на низьких швидкостях різання (V = 4... 12 м/мін), тобто до появи області наросту. Тим не менш, завдяки великому числу зубів продуктивність при розгортанні досить висока, так як машинне час зменшується за рахунок збільшення числа зубів Для отримання високої точності отворів розгортки виготовляють з більш жорсткими допусками, ніж зенкери, а отвори під розгортання отримують свердлінням, зенкерованием або растачиванием. Розгортання безпосередньо після свердління використовують тільки при обробці отворів невеликих діаметрів. Розгортки класифікують за такими ознаками: за видом привода - ручні та машинні;
за способом кріплення - хвостові і насадні;
по вигляду оброблюваного отвору - циліндричні та конічні;
по виду ріжучого матеріалу - швидкорізальні, твердосплавні та алмазні;
за типом конструкції - цілісні і збірні (зі вставними ножами).
Фрези
Фрези - це багатозубі ріжучі інструменти, що застосовуються для обробки площин, пазів, фасонних поверхонь, тіл обертання, а також для розрізання матеріалів. В процесі фрезерування в контакті із заготовкою, як правило, знаходиться кілька зубів, знімають стружку змінної товщини. При цьому завдяки великій сумарної активної довжини різальних кромок забезпечується висока продуктивність процесу фрезерування. Підвищенню продуктивності сприяє висока швидкість фрезерування, яка досягається за рахунок періодичного виходу зубів із зони різання, що забезпечує охолодження і зняття теплової напруженості в ріжучому клині. Кінематика фрезерування проста: фреза отримує обертання від головного приводу, а заготовка, закріплена на столі верстата, - рух подачі від окремого приводу верстата, кінематично не пов'язане з обертанням фрези. Рух подачі може бути прямолінійним, обертальним або гвинтовим, а ріжучі кромки фрези - прямолінійними, похилими до осі, гвинтовими або фасонними. Це зумовило появу величезної різноманітності конструкцій фрез і широку область їх застосування. Фрези можна класифікувати за такими основними ознаками: 1) конструкція ріжучих зубів і спосіб їх заточування - фрези з загостреними зубцями, перетачиваемыми по задній поверхні і з затилованнимі зубами, перетачиваемыми з передньої грані; 2) форма і розташування ріжучих кромок відносно осі обертання інструменту - фрези циліндричні, дискові, торцеві, кінцеві, кутові, фасонні; 3) напрямок зубів до осі фрези - фрези прямозубі, гвинтові, з похилими зубцями; 4) спосіб кріплення на верстаті - фрези насадні з отвором під оправку і кінцеві з циліндричним або конічним хвостовиком; 5) конструкція фрези - цілісні і збірні зі вставними зубами, у тому числі з напаяними або механічно закріплюються різальними пластинами з твердого сплаву або ВТМ. Циліндричні фрези застосовуються на горизонтально-фрезерних верстатах при обробці площин. Ці фрези можуть бути з прямими і гвинтовими зубами. Фрези з гвинтовими зубами працюють плавно; вони широко застосовуються на виробництві. Фрези з прямими зубами використовуються лише для обробки вузьких площин, де переваги фрез з гвинтовим зубом не мають великого впливу на процес різання. Циліндричні фрези виготовляються з швидкорізальної сталі, а також оснащують твердосплавними пластинками, плоскими і гвинтовими. Торцеві фрези широко застосовуються при обробці площин на вертикально-фрезерних верстатах. Вісь їх встановлюється перпендикулярно обробленої площині деталі. На відміну від циліндричних фрез, де всі точки ріжучих кромок є профілюючими і формують оброблену поверхню, у торцевих фрез тільки вершини ріжучих крайок зубів є профілюючими. Торцеві ріжучі кромки є допоміжними. Головну роботу різання виконують бокові ріжучі кромки, розташовані на зовнішній поверхні. Торцеві фрези забезпечують плавну роботу навіть при невеликій величині припуску, так як кут контакту з заготовкою у торцевих фрез не залежить від величини припуску і визначається шириною фрезерування і діаметром фрези. Торцева фреза може бути більш масивною і жорсткою, порівняно з циліндричними фрезами, що дає можливість зручно розміщувати і надійно закріплювати ріжучі елементи і оснащувати їх твердими сплавами. Торцеве фрезерування зазвичай забезпечує більшу продуктивність, ніж циліндричне. Тому в даний час більшість робіт по фрезеруванню площин виконується торцевими фрезами. Кінцеві фрези застосовуються для обробки глибоких пазів у корпусних деталях контурних виїмок, уступів, взаємно перпендикулярних площин. Кінцеві фрези на шпинделі станка кріпляться конічним або циліндричним хвостовиком. У цих фрез основну роботу різання виконують головні ріжучі кромки, розташовані на циліндричній поверхні, а допоміжні торцеві ріжучі кромки тільки зачищають дно канавки. Такі фрези, як правило, виготовляються з гвинтовими або похилими зубцями. Кут нахилу зубів доходить до 30-45°. Діаметр кінцевих фрез вибирають меншим (до 0,1 мм) ширини канавки, так як при фрезеруванні спостерігається розбивання канавки. Різновидом кінцевих фрез є шпонкові двох-зубые фрези. Розглянуті шпонкові фрези, подібно свердла, можуть заглиблюватися в матеріал заготовки при осьовому русі подачі і висвердлювати отвір, а потім рухатися уздовж канавки. У момент осьової подачі основну роботу різання виконують торцеві кромки. Одна з них повинна доходити до осі фрези, щоб забезпечити свердління отвору. Переточування шпонкових фрез здійснюється по задніх поверхонь торцевих кромок. При цьому діаметр фрези зберігається незмінним, що необхідно для забезпечення сталості розміру паза. Однак ці фрези володіють високою продуктивністю, незважаючи на частково зрізані зуби. Дискові фрези пазові, двох - і тристоронні використовуються при фрезеруванні пазів і канавок. Дискові пазові фрези мають зуби тільки на циліндричній поверхні і призначені для обробки відносно неглибоких пазів. Для зменшення тертя по торцях на пазових фрезах передбачається допоміжний кут в плані φ1, близько 30', тобто товщина фрези робиться на периферії більше, ніж у центральній частині маточини. Важливим елементом пазової фрези є її товщина, яка виконується з допуском 0,04—0,05 мм. По мірі сточування зубів, в результаті поднутренія, товщина фрези зменшується. Однак це не має практичного значення, так як величина зменшення невелика. Кутові фрези використовуються при фрезеруванні кутових пазів і похилих площин. Одноугловые фрези мають ріжучі кромки, розташовані на конічній поверхні і торці. Двухугловые фрези мають ріжучі кромки, розташовані на двох суміжних конічних поверхнях. Кутові фрези знаходять широке застосування в інструментальному виробництві для фрезерування стружкових канавок різних інструментів. У процесі роботи одноугло-вимі фрезами виникають осьові зусилля різання, так як зрізання металу заготовки проводиться в основному ріжучими кромками, розташованими на конічній поверхні. У двухугловых ж фрез осьові зусилля, що виникають при роботі двох суміжних кутових кромок зуба, дещо компенсують один одного, а при роботі симетричних двухугловых фрез вони взаємно врівноважуються. Тому двухугловые фрези працюють більш плавно. Для обробки Т-образних пазів, часто зустрічаються у верстатобудуванні, застосовують Т-подібні фрези Вони працюють у важких умовах і часто ламаються, що пояснюється утрудненим відводом стружки. Кожен зуб працює два рази за один оберт фрези. Фрези для обробки Т-образних пазів працюють у важких умовах і часто ламаються через пакетування стружки. Для поліпшення її відведення такі фрези роблять з різноспрямованими зубцями і з кутом поднутренія на торцях, рівним φ1 = 1...2° Фасонні фрези отримали значне поширення при обробці різноманітних фасонних поверхонь. Переваги застосування фасонних фрез особливо сильно проявляються при обробці заготовок з великим відношенням довжини до ширини фрезерованих поверхонь.
Резьбообразующие інструменти
У техніці використовуються різноманітні типи різьб. Найбільшого поширення набула циліндрична різьба. За формою профілю різьби бувають трикутні, трапецієподібні, прямокутні, радіусні та ін. Різьби можуть бути однозаходные і многозаходные, зовнішні і внутрішні, праві і ліві. В даний час при обробці різьблення різанням найбільш широке поширення отримали дві схеми обробки, одна з яких відповідає точіння, а друга — фрезеруванню.
Різьбонарізні фрези
У практиці машинобудування застосовуються наступні основні види різьбонарізних фрез: гребінчасті, дискові та головки для вихрового нарізування різьби. Застосування фрезерування замість точіння при нарізуванні зовнішньої і внутрішньої різьби забезпечує значне підвищення продуктивності за рахунок: 1) використання многозубого інструменту з великою сумарною довжиною активної ріжучих крайок, одночасно знімають стружку (гребінчасті фрези); 2) збільшення товщини зрізу на один зуб (дискові фрези); 3) збільшення швидкості різання за рахунок оснащення різців твердим сплавом (головки для вихрового нарізування різьби). Гребінчасті фрези застосовуються для нарізування гострокутних зовнішніх і внутрішніх різьб з дрібним кроком на циліндричних і конічних поверхнях заготовок. По суті, вони являють собою набір дискових фрез, виконаних за одне ціле на одному корпусі з профілем зубів, відповідним профілю різьби. Тому канавки між фрезами кільцеві. Для утворення зубів вздовж осі фрези прорізані або прямі, або гвинтові стружкові канавки. Для утворення задніх кутів зуби затылуют за до архімедового спіралі.
Різьбові різці та гребінки
Різьбові різці застосовуються для нарізування всіх видів різьб і володіють наступними перевагами: простотою конструкції, технологічністю і універсальністю. Остання перевага полягає в тому, що одним і тим же різцем можна нарізати на циліндричних і конічних поверхнях зовнішню і внутрішню різьби різного діаметра і кроку. вляясь фасонним інструментом, різьбові різці можуть бути трьох типів: стрижневі, призматичні і круглі.
Гребінки - це многониточные фасонні різці, які можуть бути стрижневими, призматичними, круглими. Їх використовують головним чином для виготовлення кріпильних різьб з дрібним кроком, тобто різьб з невеликою висотою профілю.
Мітчики
Мітчики широко використовуються в машинобудуванні для нарізування різьби в отворах заготовок і вельми різноманітні по конструкціях і геометричним параметрам. Мітчик - це гвинт, перетворений в інструмент шляхом прорізання стружкових канавок і створення на ріжучих зубцях передніх, задніх і інших кутів. Для кріплення на верстаті або у воротку він забезпечений хвостовиком. Ріжуча частина мітчика виготовляється найчастіше з швидкорізальної сталі, рідше з твердого сплаву.
Достоїнствами мітчиків є: простота і технологічність конструкції, можливість нарізування різьби за рахунок самоподачи, висока точність різьби, визначається точністю виготовлення мітчиків.
По конструкції і застосування мітчики поділяють на такі типи:
1) ручні (слюсарні) - з ручним приводом, виготовляються комплектами з двох або трьох номерів;
2) машинно-ручні одинарні або в комплекті з двох номерів -з ручним або верстатним приводом;
3) машинні одинарні - з верстатним приводом;
4) гайкові - для нарізування різьби в гайках на спеціальних верстатах;
5) плашкові і маткові - для нарізування і, відповідно, калібрування різьби в різьбонарізних плашках;
6) спеціальні - для нарізування різьб різних профілів: трапецеїдальних, круглих, наполегливих і т. д., а також збірні регульовані, мітчики-протяжки, конічні мітчики та ін.
Особливості конструкцій деяких основних типів мітчиків
. Незважаючи на простоту конструкцій інструментів, у практиці знайшли застосування різні варіанти їх виконання стосовно до вирішення конкретних завдань виробництва.Нижче наведено короткі характеристики конструкцій мітчиків, що знайшли найбільше практичне застосування.
Слюсарні (ручні) мітчики призначені для нарізування різьби вручну. Вони виготовляються з інструментальних сталей комплектами з двох або трьох мітчиків, у яких різьба отримана накаткою роликами. Клас точності мітчика невисокий (4-й клас).
Машинні та машинно-ручні мітчики використовуються на свердлильних, токарних і агрегатних верстатах для нарізання метричної різьби М2...М24 в заготовках із сталі міцністю до 800 МПа, латуні, чавуну, у наскрізних та глухих отворах. Розміри таких мітчиків стандартизовані. Матеріал ріжучої частини інструментів - сталь Р6М5, різьблення шліфована і затылованная. Машинно-ручні мітчики випускаються комплектами з двох або трьох номерів і можуть використовуватися також при нарізуванні різьби вручну.
Мітчики з шаховим розташуванням зубів рекомендується використовувати для нарізування різьби у в'язких матеріалах, так як вони виключають заклинювання витків інструменту в процесі різання внаслідок зменшення сил тертя. При цьому зрізання зубів мітчика здійснюється зазвичай тільки на його калібруючої частини. При обробці малопрочных в'язких матеріалів зуби зрізаються як на 1/3 довжини забірної частини, так і по всій її довжині. Практика показує, що ефект зменшення сил тертя тим вище, чим більше крок різьби.
Мітчики з укороченою стружкової канавкою або, як їх часто називають, бесканавочные мають короткі канавки змінної глибини з кутом нахилу дна канавки до осі ψ = 5...10° і осьовим кутом λ = 9...12°. Порівняно із звичайними мітчиками ці мітчики з-за великого поперечного перерізу більш міцні. Довжина канавок приблизно дорівнює подвоєній довжині забірного конуса. Щоб уникнути підвищеного моменту тертя з-за відсутності канавок на більшій довжині незатылованной калібруючої частини роблять велику зворотний конусність по зовнішньому діаметру (до 0,2 мм на 100 мм довжини).
Такі мітчики рекомендується застосовувати для нарізування різьб діаметром до 10 мм в наскрізних отворах заготовок із важкооброблюванихлегованих сталей, в'язких низьковуглецевих сталей, кольорових металів і сплавів. Вони забезпечують також високу точність і малу шорсткість поверхні різьби.
Мітчики з гвинтовими канавками, як було показано вище, рекомендуються для надійного видалення стружки в основному з глухих отворів. При нарізуванні різьб у наскрізних отворах видалення стружки в напрямку подачі мітчика простіше забезпечити шляхом загострювання передній поверхні під кутом осьовим
Ступінчасті мітчики мають подвійну ріжучу частину і дозволяють реалізувати в одному метчике будь-яку комбінацію схем різання. Наприклад, перша частина, що має заниження за профілем, може обробляти різьблення за генераторною схемою, а друга - за профільною. При цьому можна нарізати високоточні різьби. Ця конструкція зручна і для таких комбінованих схем, в яких одна частина виконує різання, а друга - вигладжування різьби.
Мітчики з ріжучо-выглаживающими зубами мають пір'я з ріжучими і провідними ділянками. Канавки, які розділяють ріжучі та провідні частини мітчика, служать для підведення СОЖ і виходу абразивного круга при шліфуванні профілю різьби.
Мітчики з напрямними частинами застосовуються для обробки деталей з точним взаємним розташуванням поверхонь декількох отворів. У мітчиків для наскрізних отворів напрямна частина розташовується попереду ріжучої частини, а для глухих - після калібруючої частини. Напрямна частина, розташована після калібруючої частини, має збільшений діаметр і вимагає застосування кондукторной втулки.
Мітчики з внутрішнім підведенням МОР мають стійкість у 3...4 рази вище за кращих умов охолодження, змащення і відводу стружки, але вимагають спеціальних пристроїв для підведення СОЖ.
Мітчики дзвонового типу застосовують при нарізуванні різьб у наскрізних отворах великих діаметрів d = 50...400 мм у важкому машинобудуванні. Вони виконуються цільними або складовими. В останньому випадку робоча частина мітчика насадна, що складається з ріжучої та калібруючої частин. Внутрішня порожнина мітчика забезпечує підведення СОЖ і має великий простір для розміщення стружки. Кількість пір'я у таких мітчиків доходить до 16.
Гайкові мітчики служать для нарізування наскрізних різьб без згвинчування гайок шляхом їх нанизування на хвостову частину. Для кращого заходу мітчика в отвір вони мають довгу забірну і коротку калібруючу частини.
З-за великої довжини гайкових мітчиків, що утрудняє їх виготовлення, особливо при шліфуванні різьби, їх часто роблять складовими: окремо виготовляють ріжучу і хвостову частини, а потім їх з'єднують зварюванням тертям, паянням або за допомогою різьби.
Хвостовики гайкових мітчиків виготовляють довгими прямими або вигнутої форми. Мітчики з вигнутими хвостовиками застосовують для нарізування різьби в гайках на верстатах-автоматах з безперервним циклом. Тут заготовки гайок подаються з бункера в зону різання і після нарізування різьби сходять по вигнутому хвостовика в лоток
Конічні мітчики. Особливість роботи конічних мітчиків полягає в тому, що нарізування різьби відбувається по всій довжині мітчика, рівній довжині різьби. Калибрующая частина у конічних мітчиків відсутня, що сприяє появі великих зусиль різання. Нарізування різьби, як правило, проводиться на верстатах з запобіжним пристроєм, що спрацьовує в кінці різання. Основні параметри мітчиків подібні параметрами мітчиків для циліндричних різьб.
Мітчик-протяжка дозволяє нарізати в наскрізних отворах різьблення будь-яких профілів і довжини, з будь-яким числом заходів. Мітчик-протяжка порівняно із звичайними мітчиками і різьбовими різцями забезпечує підвищення продуктивності в декілька разів при високій точності і низької шорсткості різьби.
Особливості конструкції мітчика-протяжки:
1) хвостовик розташовується попереду ріжучої частини і мітчик працює на розтяг; 2) робоча частина мітчика представляє собою конічну поверхню великої протяжності із зубами, профіль яких відповідає профілю нарізати різьблення; 3) зуби по середньому діаметру не затылуются, а заточуються тільки по задніх поверхнях з подвійною заточкою; 4) ширина ріжучих кромок по зовнішньому діаметру мінлива. Вона зменшується від перших зубів до останніх, тобто використовується генераторна схема різання; 5) стружкові канавки виконують гвинтовими: для правої різьби - ліві, для лівої різьби - праві; 6) у кінці робочої частини мітчика іноді передбачають коротку калібруючу частину і задній хвостовик.
Нарізування різьби зазвичай проводиться на токарному верстаті з n = 18...40 об/хв і v = 2...3 м/хв. Хвостовик мітчика з допомогою клина кріплять на супорті верстата. Перед протягуванням заготівлю надягають на мітчик і затискають в самоцентрирующем патроні верстата і приводять в обертання. При цьому шпиндель верстата включають на зворотний хід і супорт переміщується вправо з подачею на один оборот, що дорівнює кроку нарізати різьблення.
При нарізуванні різьби у високоміцних матеріалах робочу частина мітчика-протяжки ділять на сходи. При цьому кожна ступінь має ріжучу і калібруючу частини, а проточки між східцями служать для виходу стружки.
Плашки
Резьбонарезная плашка - це гайка, перетворена в ріжучий інструмент шляхом свердління стружкових отворів і формування на зубцях ріжучих пір'я передніх і задніх кутів. Плашки застосовують для нарізування зовнішніх різьб на болтах, гвинти, шпильки та інших кріпильних деталях. За формою зовнішньої поверхні плашки бувають: круглі, квадратні, шестигранні, трубні. Для слюсарних робіт вони роблять розрізними і затискаються в воротках. Саме широке застосування знайшли плашки круглі, як найбільш технологічні і прості в експлуатації. Вони виготовляються з каліброваних прутків швидкорізальної сталі на токарних пруткових верстатах-автоматах.
Плашки для конічних різьб застосовуються при нарізуванні зовнішніх різьб в трубопроводах високого тиску. Особливості конструкцій таких плашок: 1) плашки працюють не напроход, а тільки з одного боку, має забірний конус з кутом 2φ = 30...55°; 2) пір'я роблять як можна меншої ширини для зниження сил різання і тертя; 3) число стружкових отворів zc = 4...7, d= 1/6...2"; 4) кути ріжучих зубів γ = 20°, α = 6°.
Найбільше навантаження на плашку виникає в кінці нарізування різьби. Щоб уникнути поломок таких плашок необхідно застосовувати патрони з запобіжним пристроєм від перевантаження.
Різьбонарізні головки
Вони мають досить широке застосування при нарізуванні частіше зовнішніх і рідше внутрішніх різьб на гвинтах, болтах, трубах та інших деталях. Ці головки являють собою досить складні збірні конструкції з ріжучими елементами у вигляді круглих гребінок або плоских плашок, встановлених у корпусі головки.
Інші статті
- Все про обладнання для механічної обробки металівПро металообробному обладнанні короткоПовна версія статті